We would like to share some of the obstacles and results from one of our more unique and challenging woodworking projects.
What made this particular project so challenging was that we weren’t going to be replacing entire cabinetry in a typical, mostly square-roomed, full-walled kitchen. This was a dome house built by the owners almost 30 years ago. The main structure was built by having approximately twenty, 4-foot wide walls all adjoined to make a circle. The roof of the structure was set on top of these walls at about 4 feet above the main floor of the structure, to form the dome.
With a typical kitchen, the boxes are joined together at the sides to form a string or row of cabinets. You take a measurement of the wall and build cabinets to match that length. Here the boxes were only joined together at the face, 24 inches from the walls. Since the basic shape of the house was circular, the walls where each of the cabinet boxes were to be installed was longer than the face of the cabinets.
Our designers measured and designed the boxes to seamlessly fit together by using mock-ups and the existing cabinets as a rough guide—not necessarily an easy task. Once the boxes were designed and constructed, the use of equal-sized spacers between each box allowed for a fairly smooth installation.
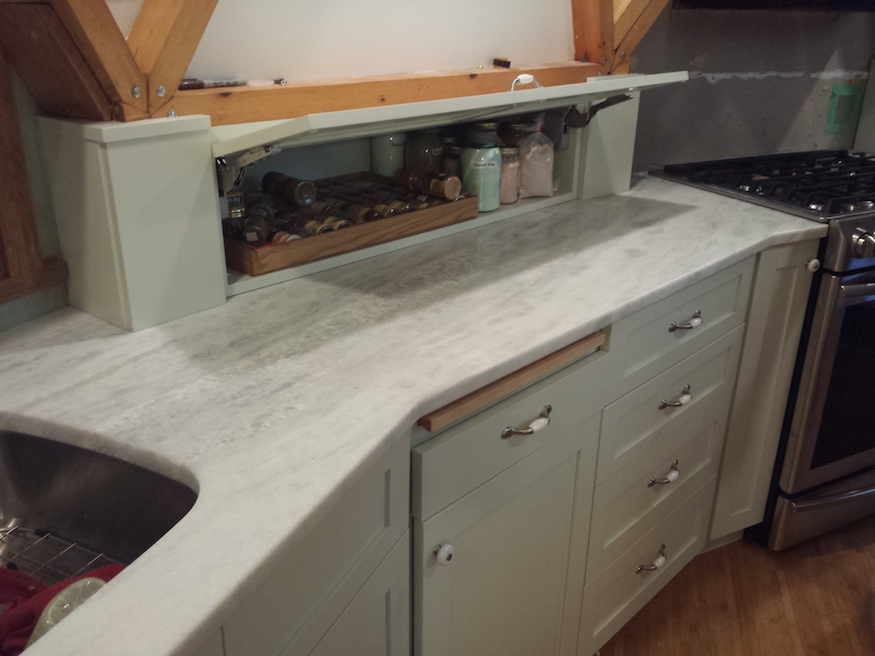
Please note that even though the existing boxes served as a guide for us to build the new cabinets, many improvements and upgrades had to be incorporated in the finished product. And while there were no wall or upper cabinets in this kitchen, the job was far from complete.
Keep in mind also that the builders of this domicile were not expert or seasoned homebuilders—they were the owners—and for such novice builders, they actually did a pretty remarkable job.
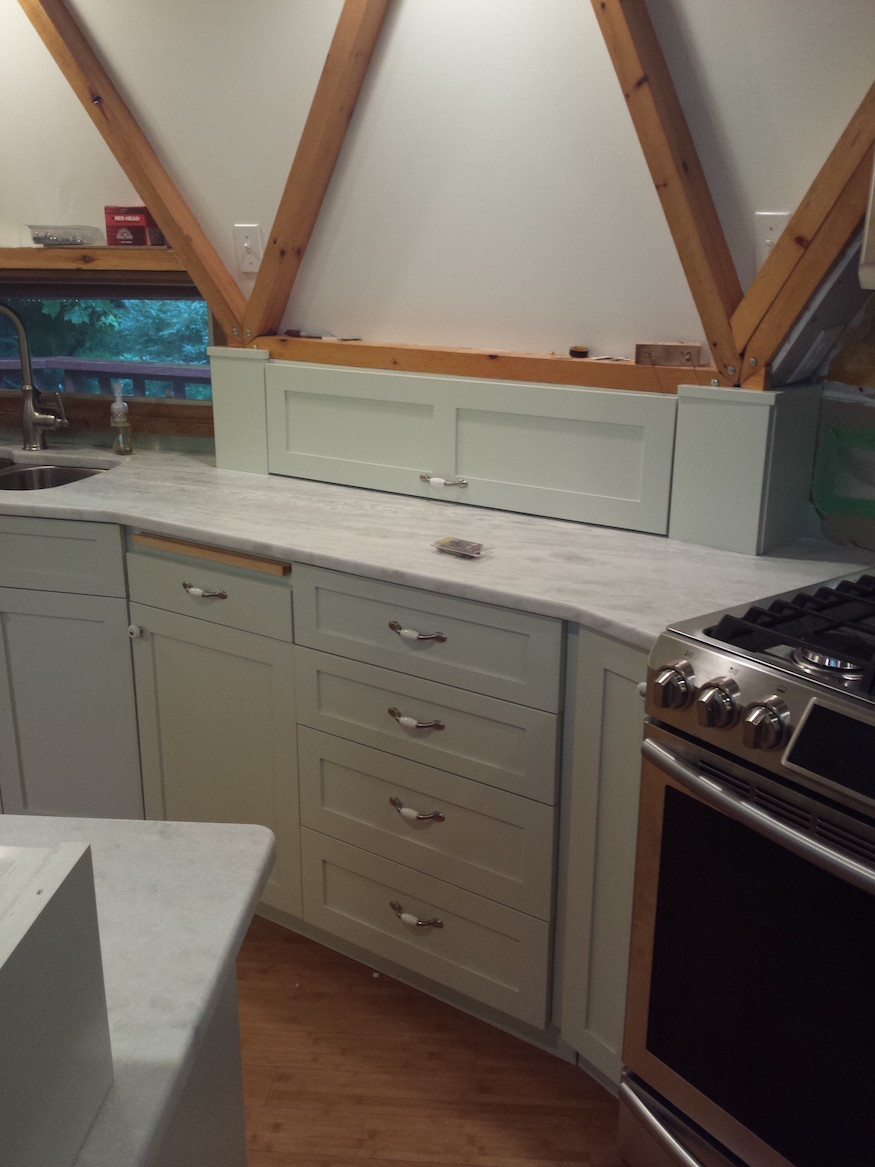
The walls were pretty well plumb and the floor was surprisingly level. But there were issues of the angle of every wall to each adjacent wall not being uniform, as well as the height of where the roof structure tied into the walls. And given the fact that we were to construct “cubbies” or garages that were to be built into the wall above the marble countertops (see picture), along with the fact that at each “corner” a column had to be custom built to cover the structural, rough-sawn posts, the word “custom” really took on a whole new meaning.
So, once the base cabinets and countertops were installed, the second and most challenging phase of the project began; the building of the “cubbies”, finishing and covering the structural posts at each corner, and not to mention installing a butcher block counter serving as a baking station.
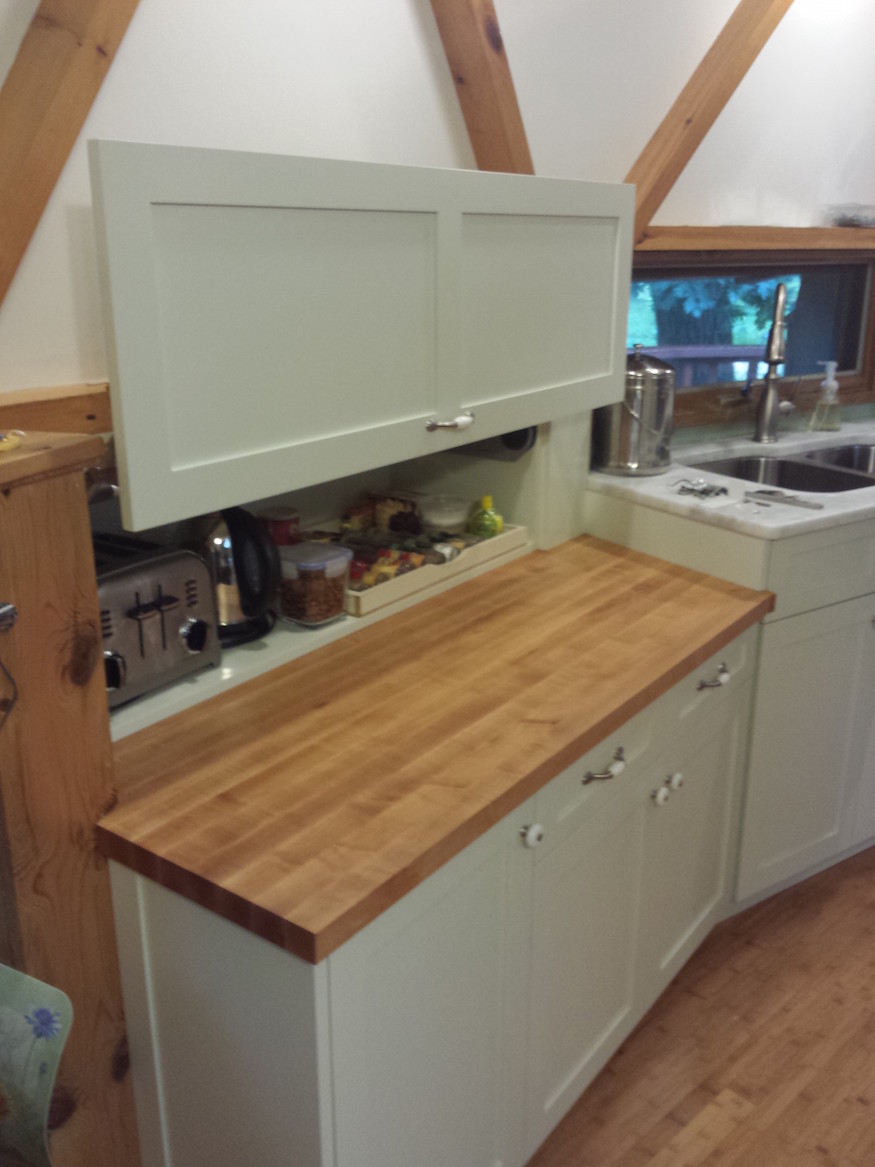
To make a long story short, every single piece of wood, door, filler and spacer had to be custom cut and fitted, often multiple times to ensure a precise and exact fit. Since it was a painted finish, several trips had to be made to create each piece and return it to the shop to be painted and brought back to be installed. It was time-consuming and at times a little maddening, but the finished results have been well worth it.
This project took the expertise of each one of our employees working together to solve potential problems and deliver a product that not only the customer deserved, but also one that everyone at D.P. Juza could and should be proud of.
Contact us today to get started on a custom woodworking project of your own for your home, office, or retail space.