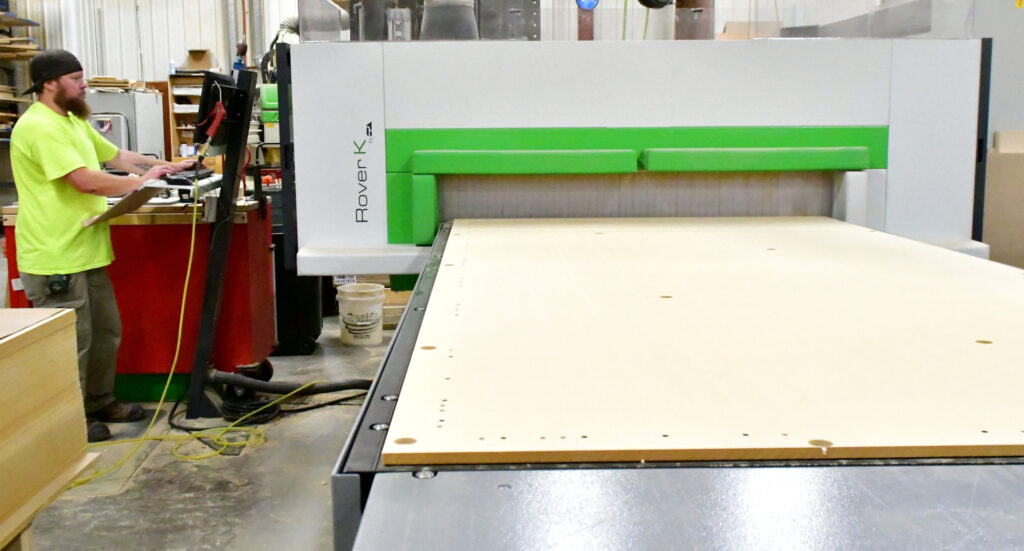
The Biesse Rover K FT CNC is an essential manufacturing tool that improves our custom fixture manufacturing process. It uses highly customizable software to control various machine tools, allowing for precise creation of parts from wood materials.
Key Features
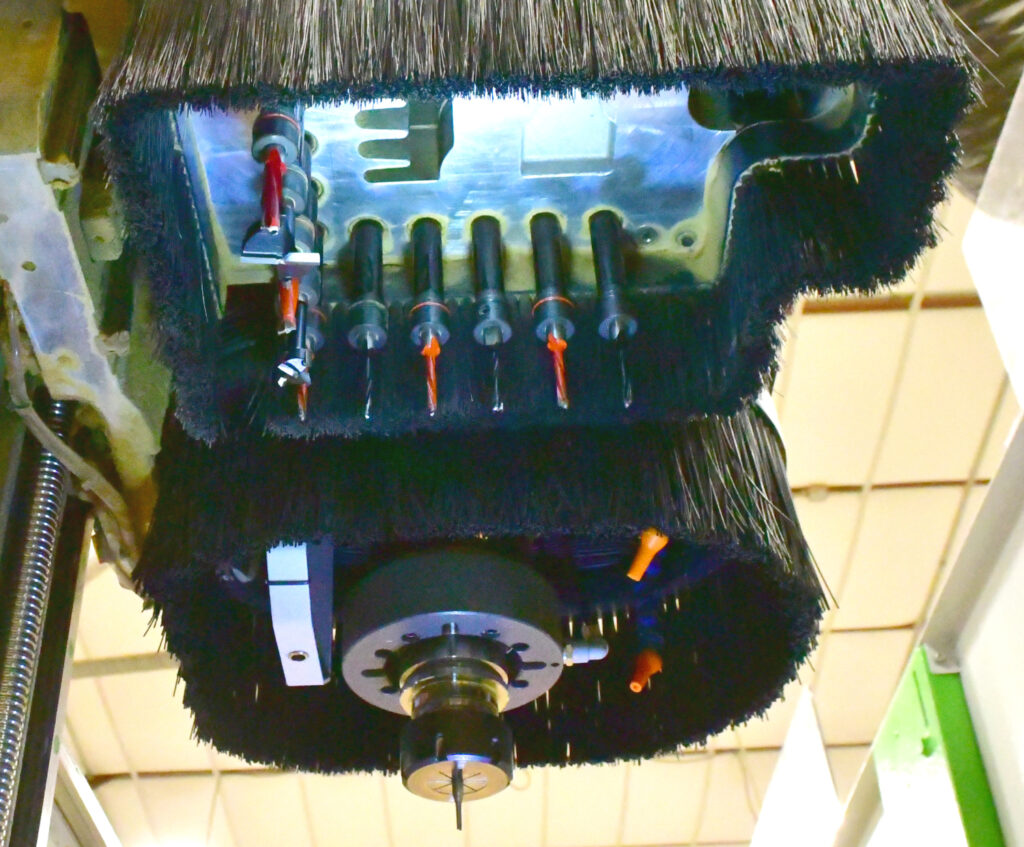
- Primary Materials: We typically use MDF with this CNC because of its machining efficiency. We also use veneered MDF, pre-finished maple plywood, and occasionally hardwood.
- Versatility: This CNC holds up to 20 cutting and boring tools, enhancing operational efficiency, and expanding cutting capabilities. Tool sizes range from 1/16th to 76.2 mil, with the spindle speed reaching a maximum of 18,000 rpm.
- Dust Management: An integrated dust collection system minimizes wood dust during operations, promoting a cleaner workspace.
- Table Dimensions: With a 5′ x 10′ table and a maximum material size of 61″ x 121″, this CNC can handle sizable projects effectively.
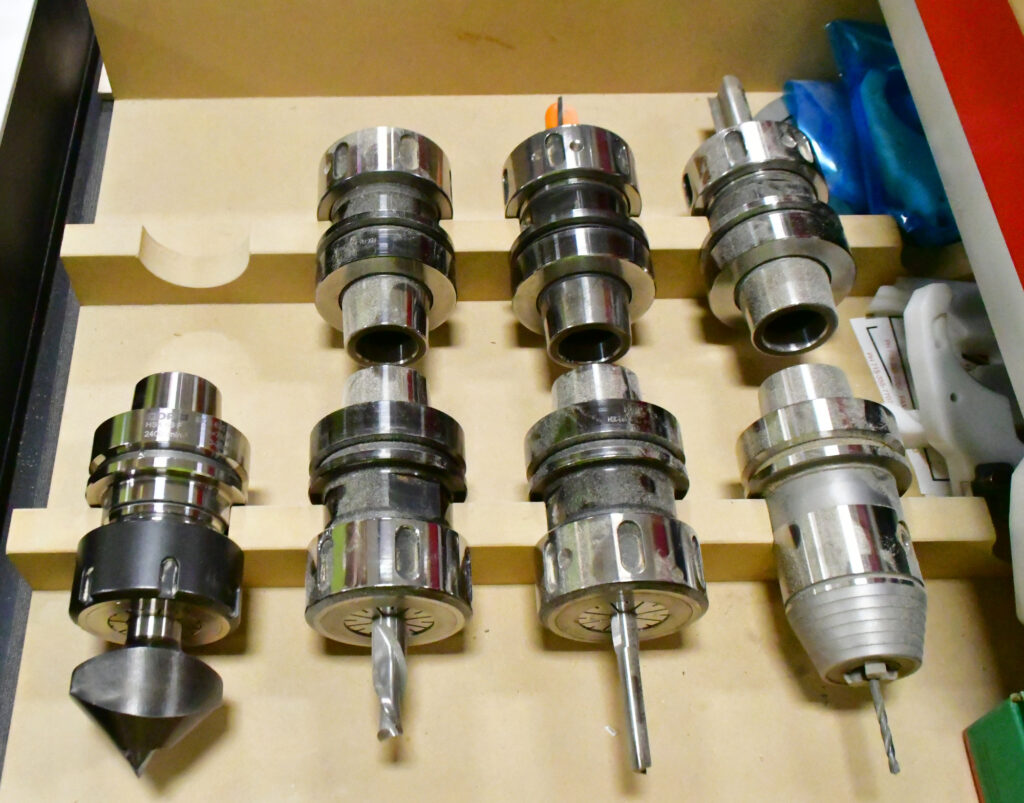
Benefits of Adding the Biesse Rover K FT
Adding the Biesse Rover K FT CNC into the DPJ shop has significantly increased production rates and the part size accuracy of our custom fixture manufacturing. Our previous reliance on a Putsch vertical panel saw and a Biesse Rover 22 CNC often resulted in inconsistently sized parts, leading to increased labor. The Rover K FT streamlines this process, ensuring precision from design to production.
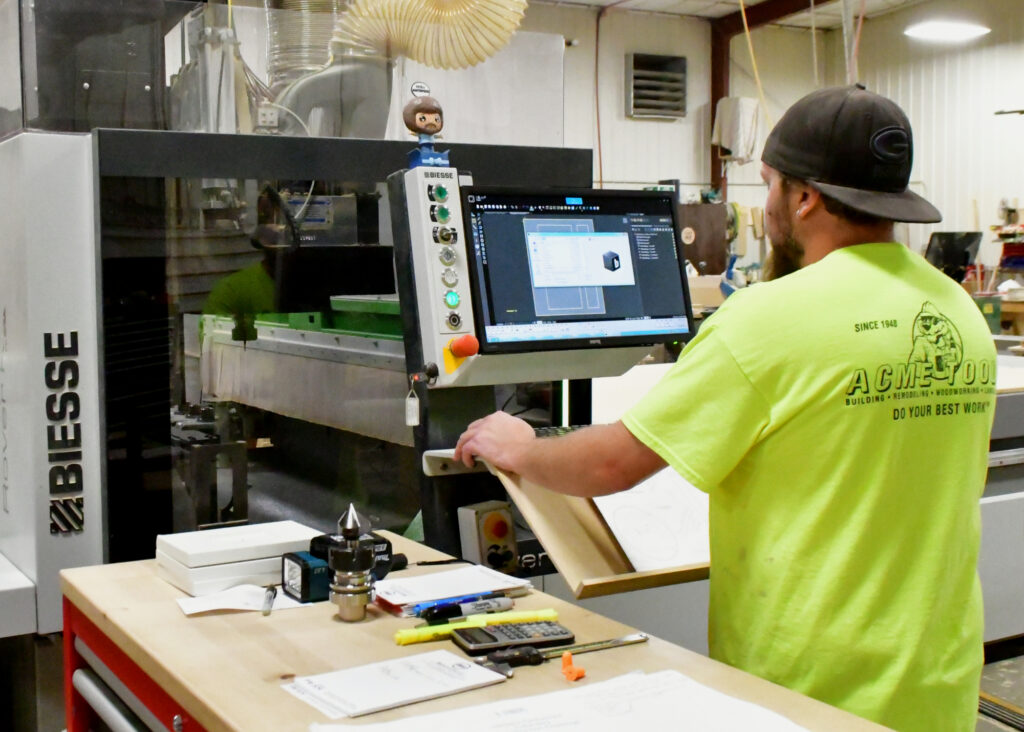
From Job Print to Cut Parts
Making a fixture from a job print to a cut part is a six-step process.
- Part Sizing: The process begins by determining the dimensions of all the parts for the fixture based on the job print, considering dado depths for cabinet assembly.
- CAD/CAM Design: The CNC operator uses the CNC’s CAD/CAM program to draw the parts and tool sequences. The tooling tells the CNC what tool to use on each part and the cut depth. The operator organizes the parts to cut in a specific order to improve the size accuracy of the finished parts.
- File Management: After the operator draws the parts and applies tooling, they save the file with an easily identifiable name.
- Nesting: The operator organizes each part onto a material sheet by nesting them together for optimal material usage.
- Setup: After a sheet is full of parts, the operator starts the program and indexing pins activate on the CNC’s table. The operator places the material on the table up against the pins and turns on the vacuum table, which holds the material in place during machining.
- Cutting Process: With the material in place, the CNC cuts the parts, which are then labeled and stored on carts until they are ready for assembly into cabinets.
The Biesse Rover K FT CNC enhances the efficiency of DPJ’s operations while ensuring high accuracy. Using this CNC significantly improves our overall manufacturing process. To maintain the optimal operation of the CNC, the operator does a maintenance routine once a month.